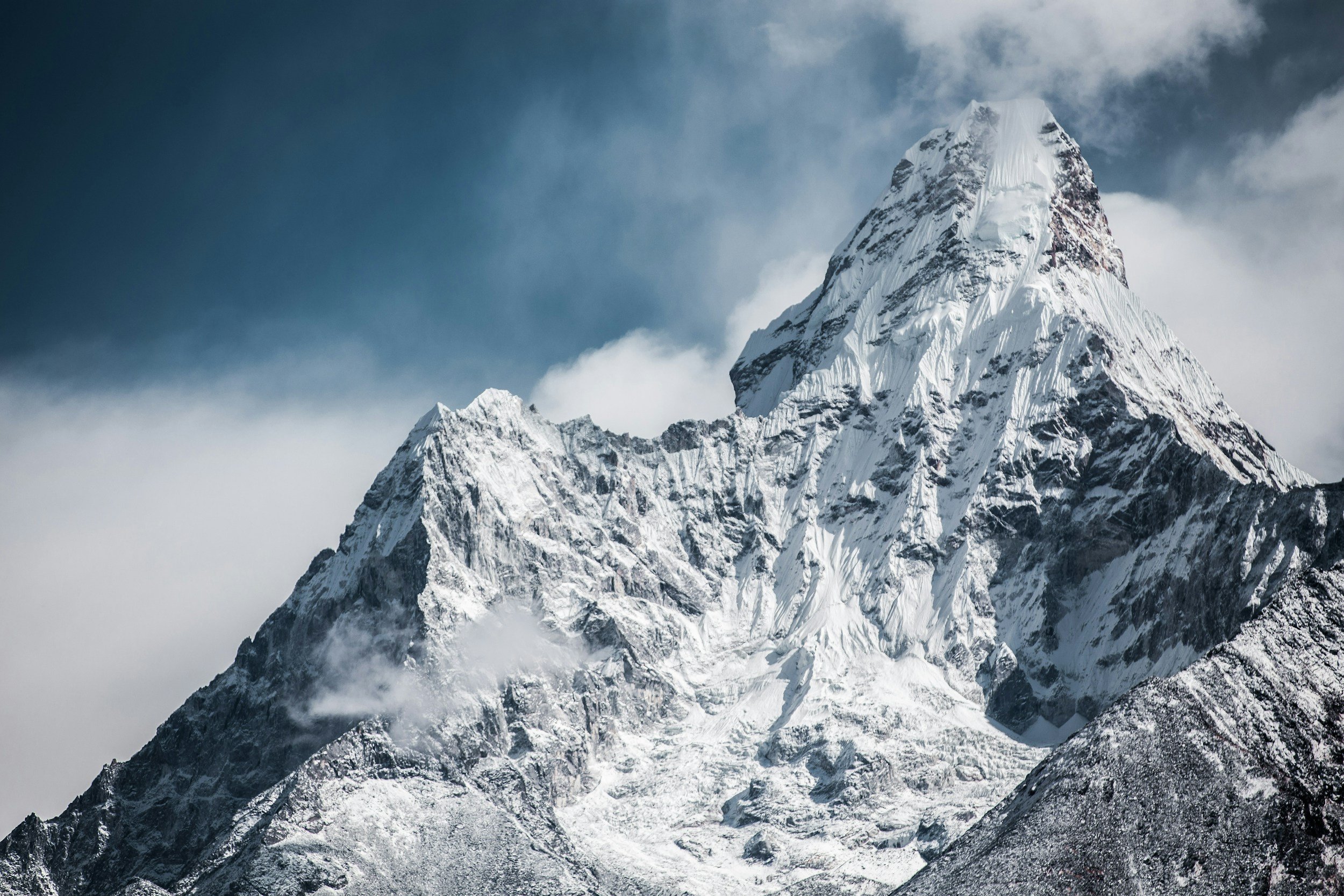
Peak performance delivered
Running a manufacturing enterprise isn’t for the faint of heart. In competitive, capital-intensive markets, challenges often emerge when launching new products, plants, customers, technologies, or navigating geopolitical pressures, supply chain disruptions, or M&A events. When those moments come, Intillit brings the support and expertise you need.
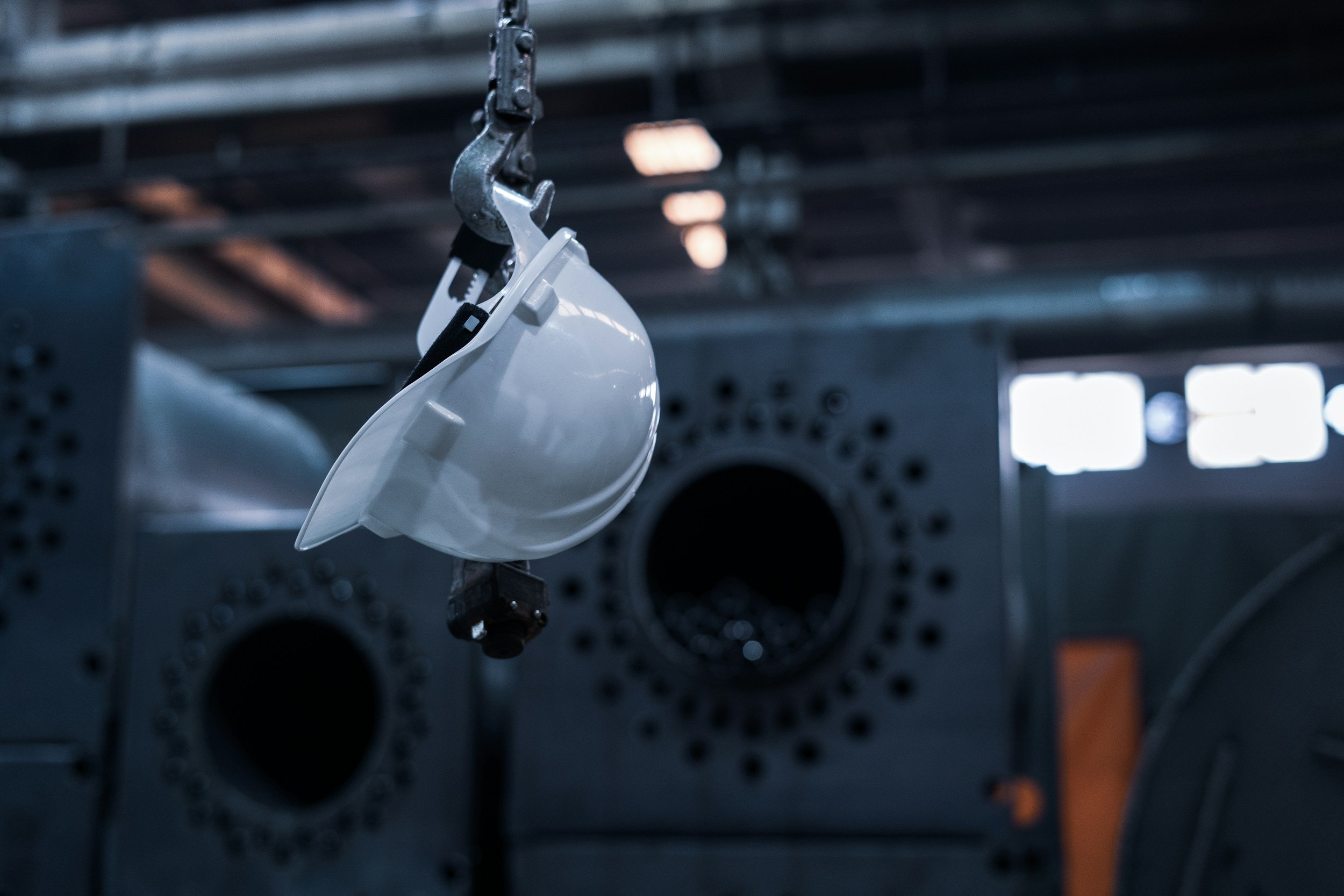
-
To us, manufacturing excellence means building strong, disciplined processes that improve overall equipment effectiveness (OEE), enhance employee retention by reinforcing the value each person brings, and elevate the customer experience through cleanliness and reliability. There is no magic bullet—no single software or specific methodology—that guarantees excellence. It’s achieved through consistent discipline, data-driven KPIs, and a hands-on approach: spending time on the floor, actively engaging with team members. Often, those closest to the work—both direct and indirect—know the problems and the solutions best.
-
From Struggling to Sustainable – When your plant is in crisis or stuck in chronic underperformance, Intillit brings rapid diagnostics and execution. We address systemic issues like chronic scrap, high unplanned downtime, and ineffective changeovers. Our playbook includes root cause analysis (RCA), stabilization of critical KPIs (e.g., yield, labor productivity, customer PPMs), and rebuilding your culture around standardized work and real-time performance tracking.
-
The Intillit team brings experience from over 40 plant launches. Launching a new facility—whether greenfield or brownfield—is an exciting opportunity that typically involves new customers and suppliers, a new location, advanced technologies (both product and process), new capital equipment, and a new workforce. However, most crises during launch stem from delays in capital spending, late hiring and training, and underdeveloped relationships with customers and suppliers. These challenges are avoidable—with the right experience, structured processes, and disciplined execution.
-
Manufacturing excellence—when it comes to processes and KPIs—is fundamentally consistent across countries. However, many companies underestimate the importance of “soft factors” and local culture. Working in Germany, Michigan, or Alabama each presents unique cultural dynamics, and the same is true for operations in Mexico. Without a deep understanding of local working culture—including the role of the cantina, transportation, medical services, and broader social factors—companies often struggle to retain talent. High turnover and constant retraining inevitably lead to declines in OEE and profitability, with potential consequences for customer satisfaction and delivery performance
-
Companies often wait too long to acknowledge they are in crisis. Egos and internal politics frequently delay critical problem-solving, which only worsens the situation. By the time the warning signs are undeniable—bleeding money from poor efficiency, rising expediting and quality costs—the business is already in financial distress, with eroding customer and employee trust.
Recovery is possible, but it requires a dedicated team focused on the top issues, guided by Pareto principles and disciplined, methodical execution. It takes people who have navigated difficult challenges before—individuals who remain calm, professional, and focused under pressure.
Organizations in denial often try to resolve the situation with their existing onsite team, which can quickly burn out and lose effectiveness. Alternatively, they send temporary "support" from headquarters—what we call “industrial tourists.” These individuals typically stay a few weeks, lack real commitment to the site, and spend more time pointing out what’s wrong than implementing solutions. Their focus is often on returning to their regular roles, making them just as ineffective.
-
When a manufacturing enterprise begins to lose value due to poor operating results, investor confidence in the company’s future cash flow and risk profile quickly erodes. In these moments, decisive action is required. While the approach may resemble that of resolving an operational crisis, the scope is broader—encompassing not just operations, but also debt and asset management, pricing strategies with customers and suppliers, leadership and ownership structures, product and production strategies, and capital allocation.
Addressing these complex challenges requires a team with no political ties—one that can remain focused on the most critical issues without distraction. Only with unbiased leadership and disciplined execution can a clear, sustainable path to recovery and renewed prosperity be defined.
-
At Intillit, we know that the best companies and teams are built on the right people. Our HR practice delivers end-to-end talent acquisition and interim HR management for manufacturing plants—securing the leadership and workforce your operation needs to thrive. Through strategic supplier cost-savings initiatives, we drive down recruitment spend without sacrificing candidate quality. Our customized training and development programs optimize both salaried and hourly roles, reducing dependency on excess staffing and boosting on-the-job performance. Seamlessly integrated into services like plant launches and turnarounds, Intillit’s HR solutions ensure your people—and your processes—are primed for success.
We are Intillit
A manufacturing and operations consulting firm. AT intillit we provide consulting and operations support to manufacturing companies worldwide. We focus on turnaround, cost optimization, program launch execution, and enterprise value creation. At Intillit we provide solutions that make the difference.
“Uncertainty is the only certainty”
-Thomas Kowal
Manufacturing’s complexities and high-stakes risks are evolving faster than ever. At Intillit, we deliver tailored strategies to help clients anticipate, mitigate, and conquer this relentless stream of challenges.

manufacturing transformation
The manufacturing industry is entering a new era—driven by geopolitical shifts, supply chain realignment, and renewed investment in North America. This moment presents a clear opportunity for the U.S. to lead with advanced manufacturing, stronger operations, and smarter use of technology. Intillit partners is built to meet this opportunity. At Intilit we work with top manufacturers to exceed standards and raise the bar within their manufacturing environment utilizing our agile, data driven teams who can execute with discipline.
Contact Us
Interested in working together? Fill out some info and we will be in touch shortly. We can’t wait to hear from you!